Practice makes perfect. Do you believe that? If that were true, wouldn’t some of us be perfect by now? Threading heddles is a repetitive activity, but intentional awareness makes it a thoughtful learning experience instead of boring repetition. This deliberate thinking produces the kind of practice that brings improvement. You mentally zoom in to see what it takes to become efficient and effective. Like practicing a musical instrument, you constantly consider how to produce the best sound (fabric) from this instrument (loom).
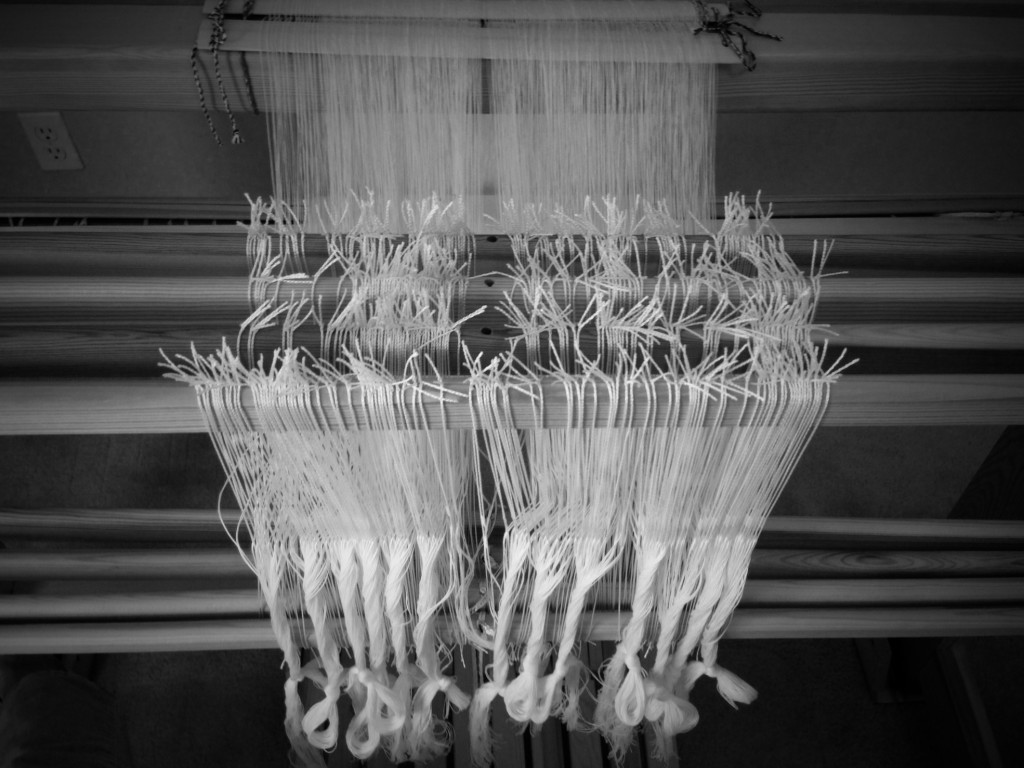
I learned to thread heddles from Leigh, and then from Joanne, and then from Becky. They each have their own approach. Their methods vary, but what they teach in common is accuracy, efficiency, and enjoyment of the process. When I thread heddles, the wealth of experience from these teachers benefits me, even as I find my own style emerging. They taught me awareness, problem-solving, and enjoyment of learning. What a gift!
Learn from the best, and then practice what you learn. Gain foundational truth. Walking in the truth is the best way to give back to your teachers. In your quest for truth, practice what you learn.
May your practice make perfect sense.
Still learning,
Karen