You are not going to believe how many knots I came across in this 16/2 linen warp! Too many. As I wound the warp I made the decision to leave most of the knots, and deal with them on the loom. (I did remove knots that were close to the beginning or ending peg on the warping reel.) I lost count, but I’m sure I have spliced the warp on this five-and-a-half-meter project at least a dozen times. (To see more details about how I splice the warp, visit this blog post and video: How To Splice the Warp – Video.)
I do not weave over warp knots. A knot introduces a spot of vulnerability to the fabric. Knots can fray, loosen, or come undone over time, even if the knot is originally imperceptible.
In a couple instances, a knot distorted the tension of the warp end because of catching on a heddle or passing through the reed. For that reason, I now try to eliminate knots in the warp before they reach the heddles.
Tool: Warp Separator
- Identify the warp end that has a knot, and insert the warp separator between warp ends to isolate the thread.
- With a length of repair warp thread, follow the path of the original thread to splice in the new warp end, feeding it through the heddle of the original warp end.
- Bring the repair warp thread through the reed in the same dent as the warp end that has a knot.
- Attach the repair warp thread near the fell by wrapping it around a flat straight pin.
- Remove the warp separator from between the warp ends.
- Place a weight on the floor below the back beam. Wrap the repair thread around the weight two or three times to hold the thread at tension that matches the rest of the warp. Loosen the wrapped-around thread before advancing the warp, and then re-tighten before resuming weaving.
- Weave one to two inches with both the original warp end and the repair warp thread in place.
- Then, cut the original warp end with the knot (behind the heddles) and let it hang over the back beam.
- The original and replacement warp ends overlap in the weaving for about one to two inches.
- Remove the straight pin when it reaches the breast beam.
- Re-attach the original warp end when it is long enough to secure in front of the fell line with a flat straight pin.
- And then, cut and remove the replacement warp thread.
- Trim all the spliced warp tails after wet finishing.
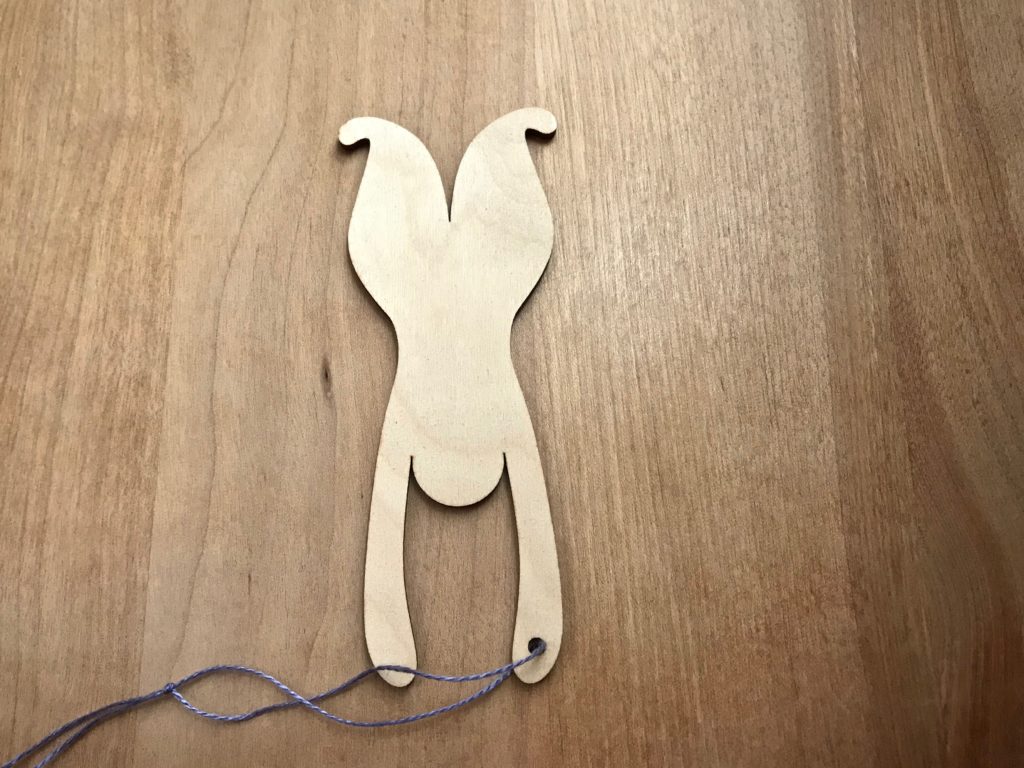
This warp separator was a gift from The Weavers and Spinners Society of Austin, included in the goodie bag from last summer’s Contemporary Handweavers of Texas Conference. It would not be hard to make a warp separator like this from wood or sturdy cardboard. I have not been able to locate a supplier online.
If you know where to find a warp separator tool, please put a link in the comments.
May you have very few warp knots.
All the best,
Karen