My looms are all occupied, so it will be a while before I can weave some new wash cloths. In the meantime, I am making “new” wash cloths to replace the ones that we have used so much that we’ve worn holes in them. The pictures tell the rest of the story.
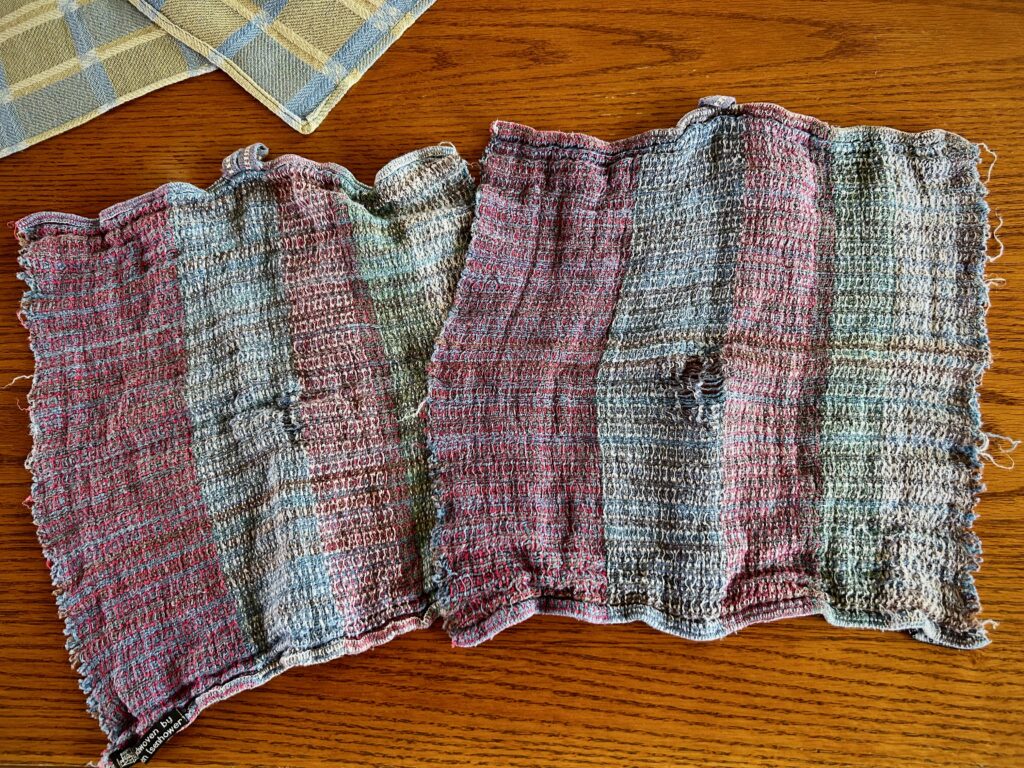
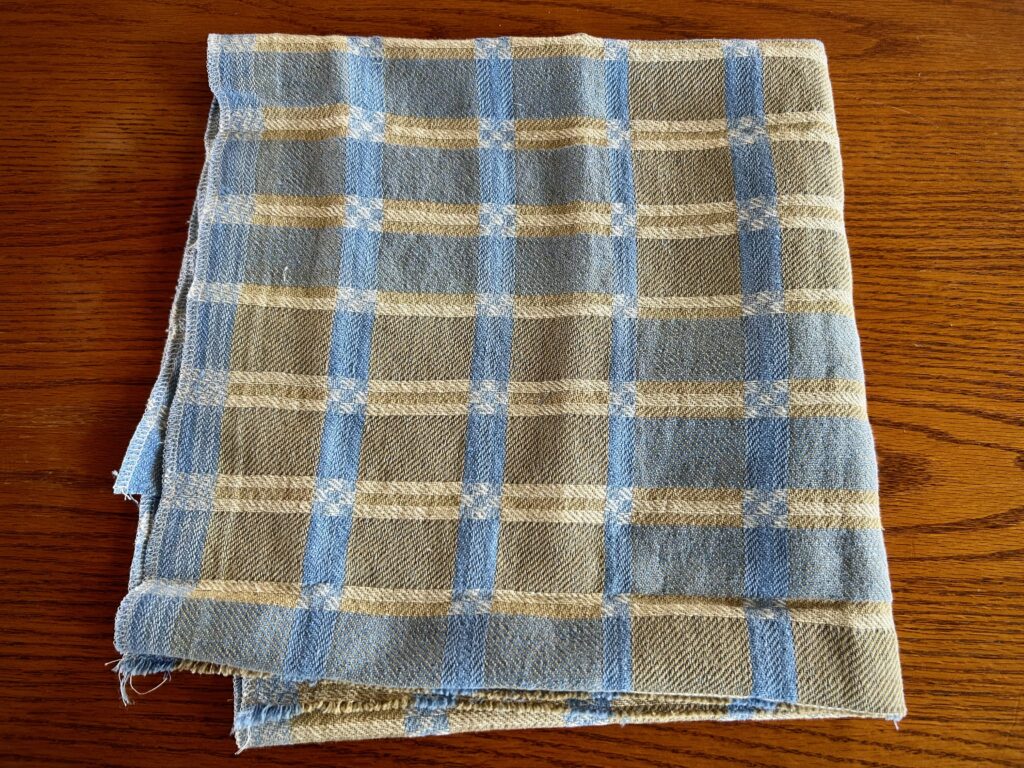
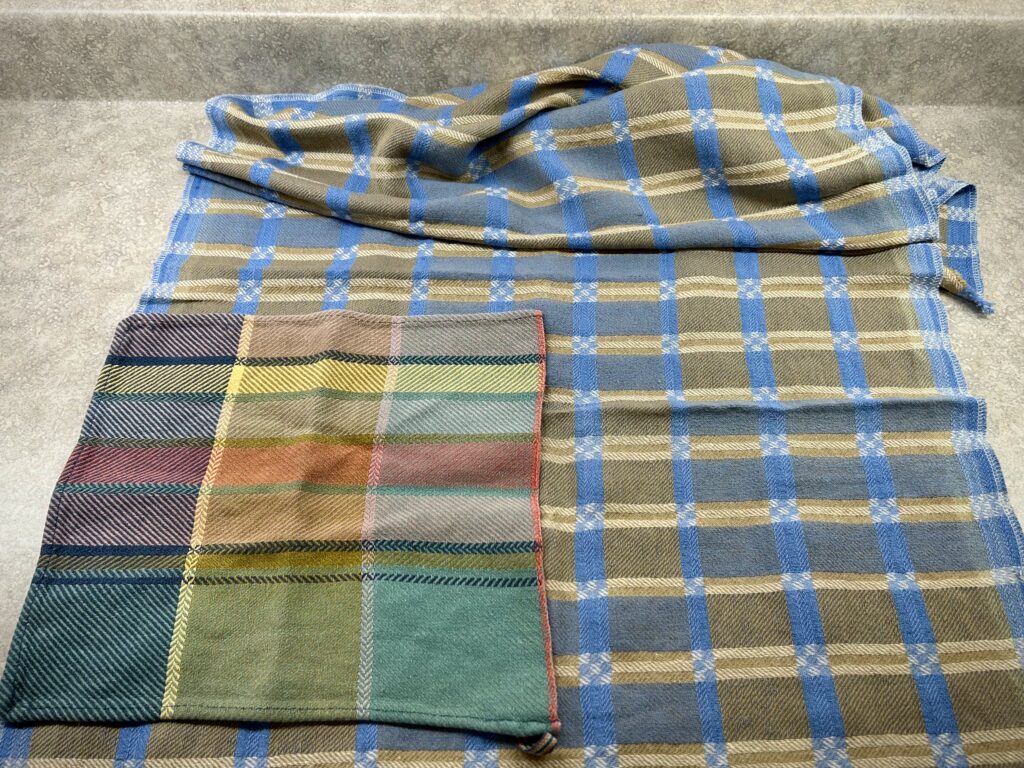
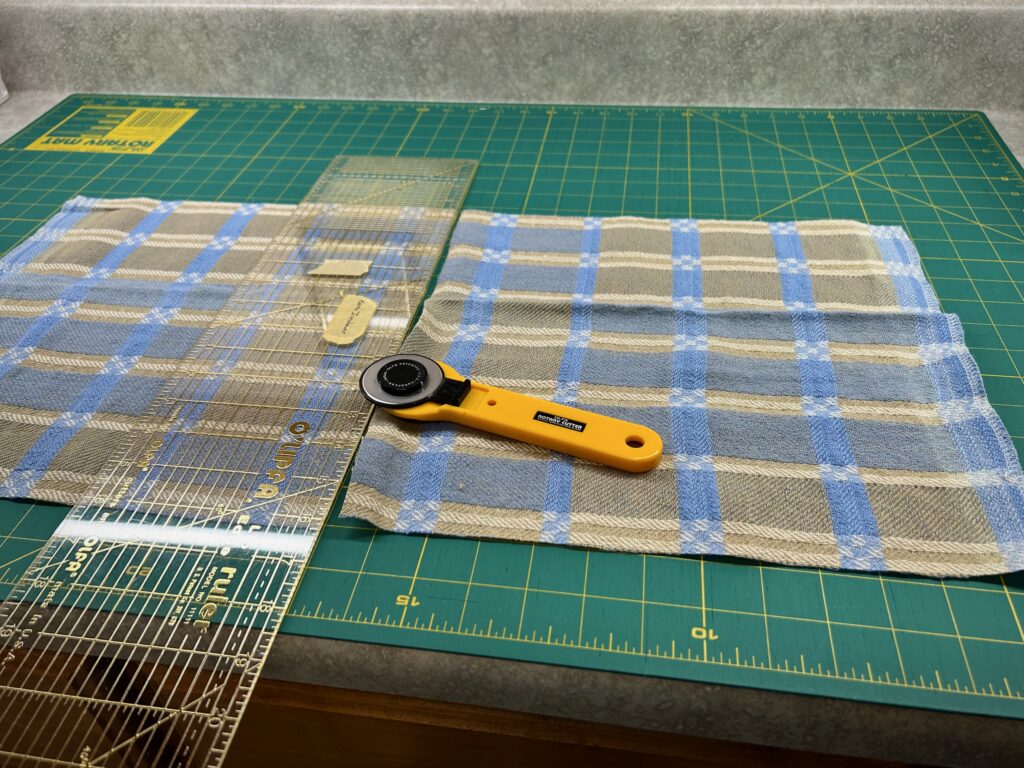

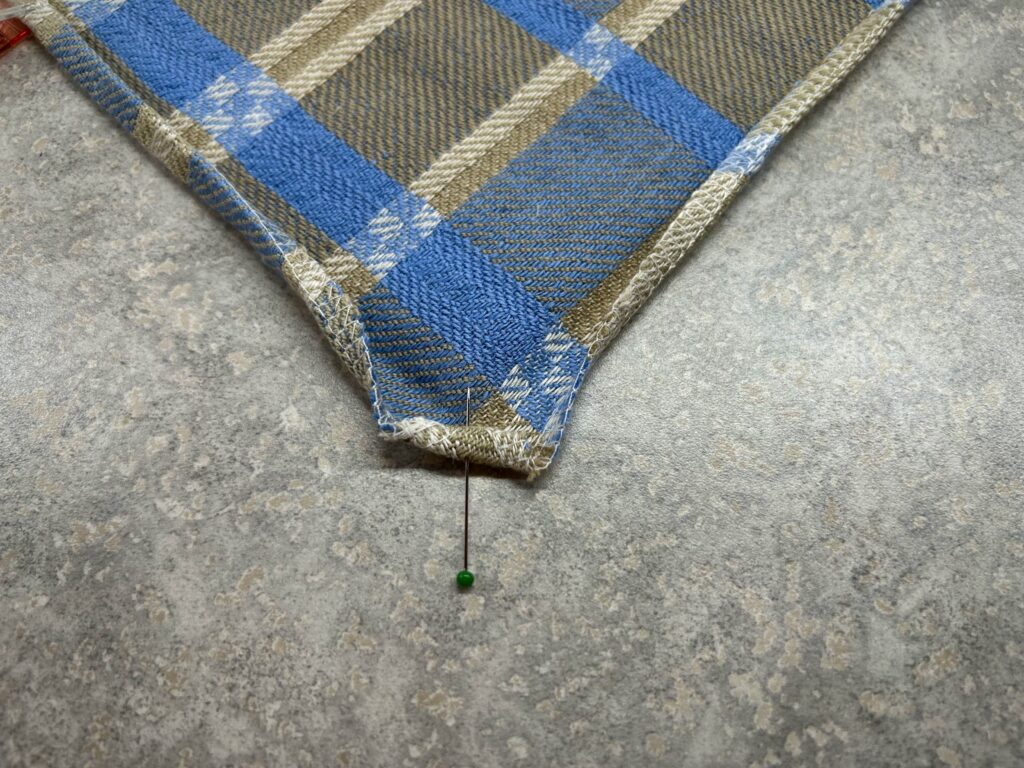
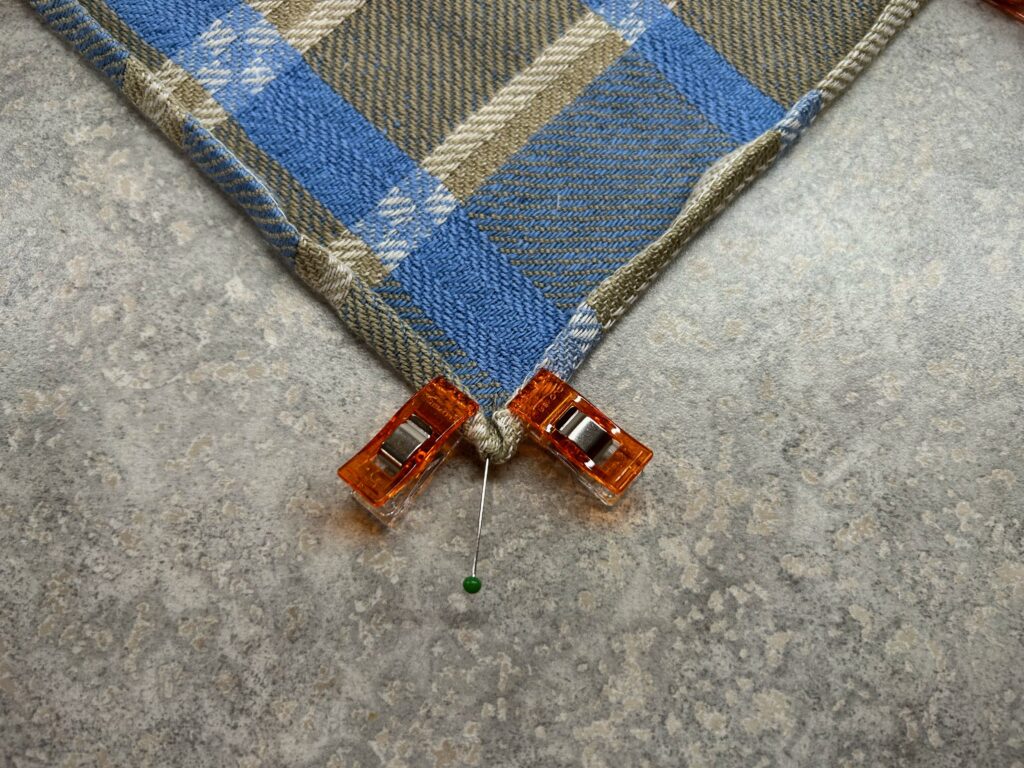
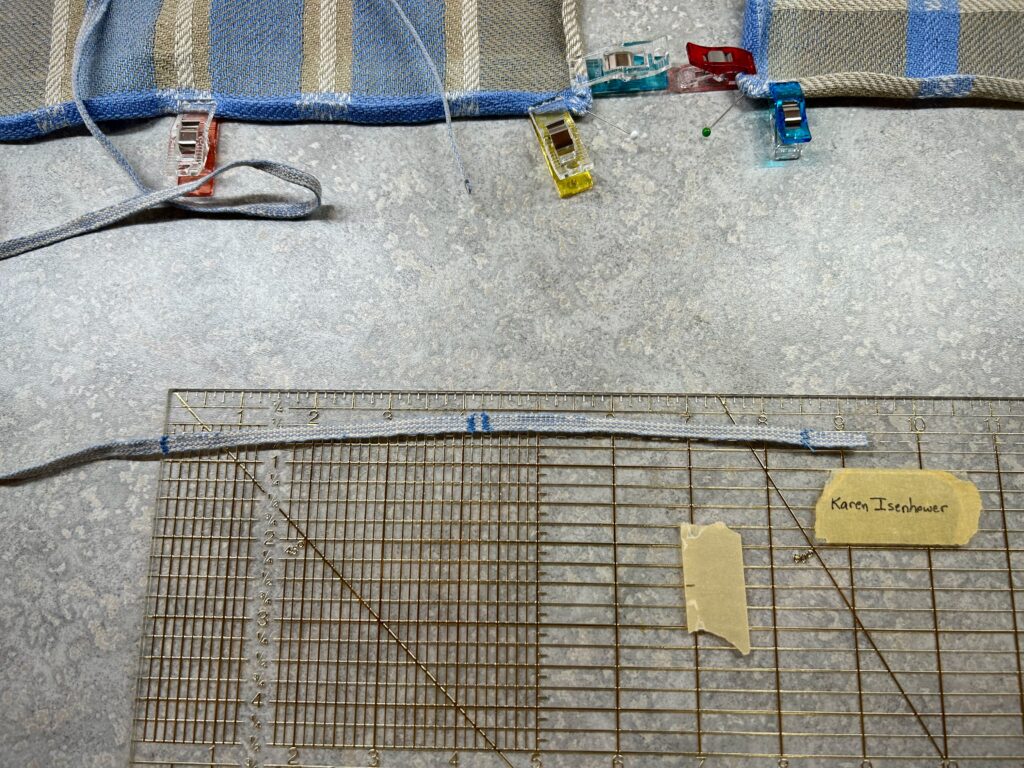
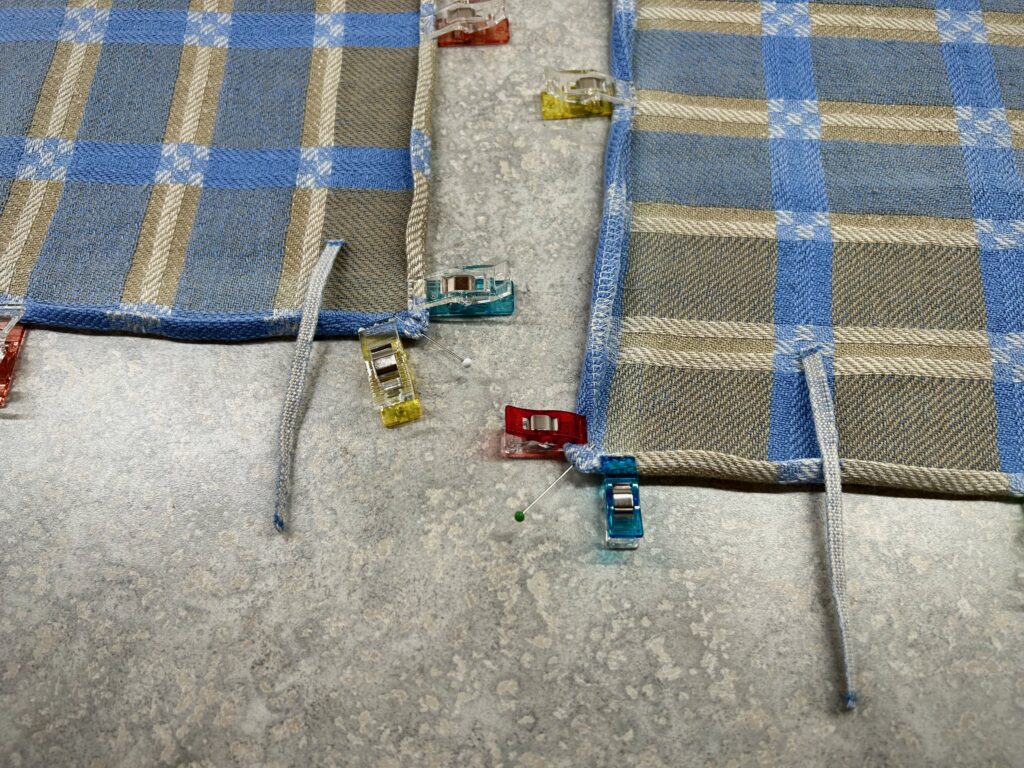
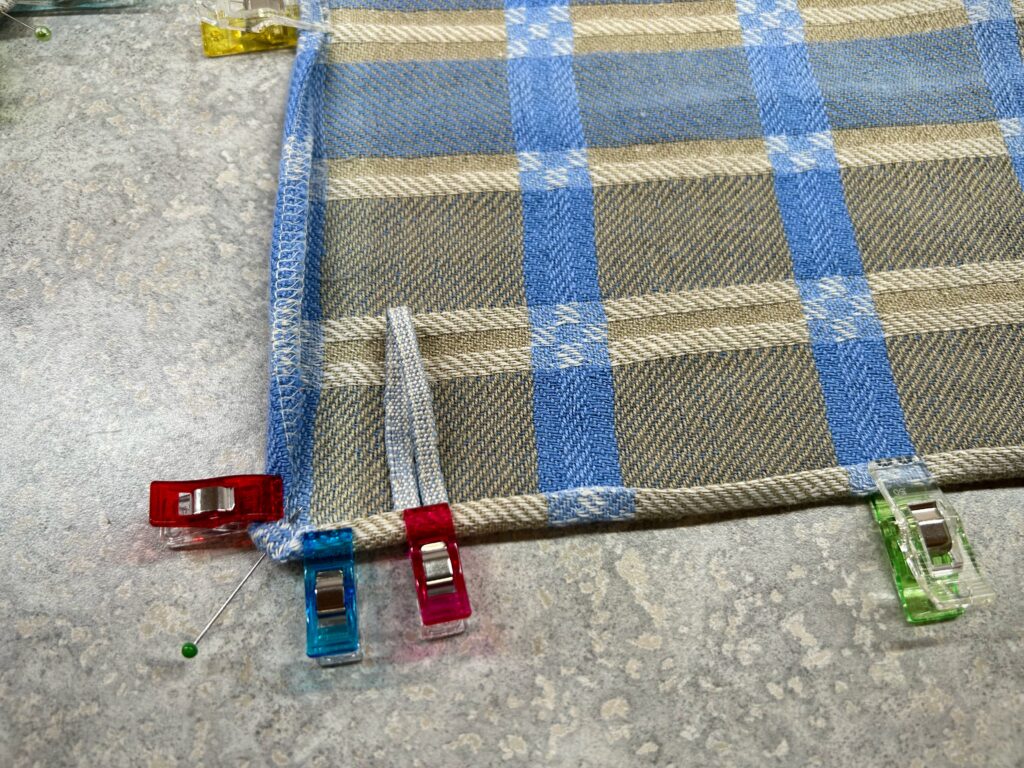
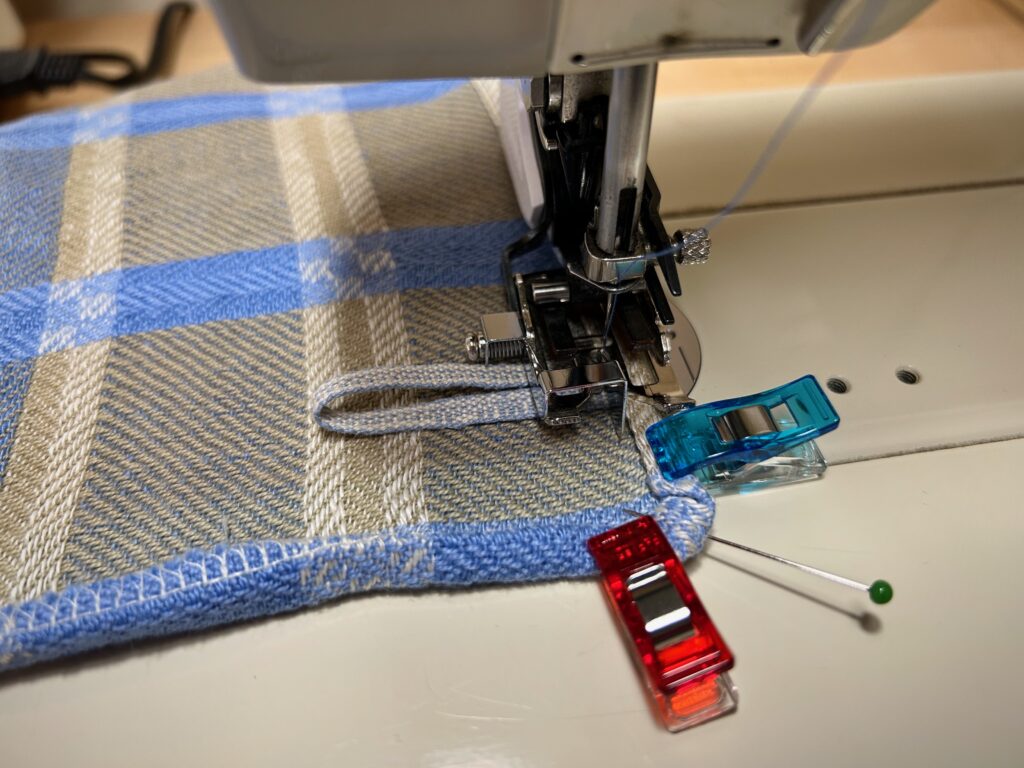

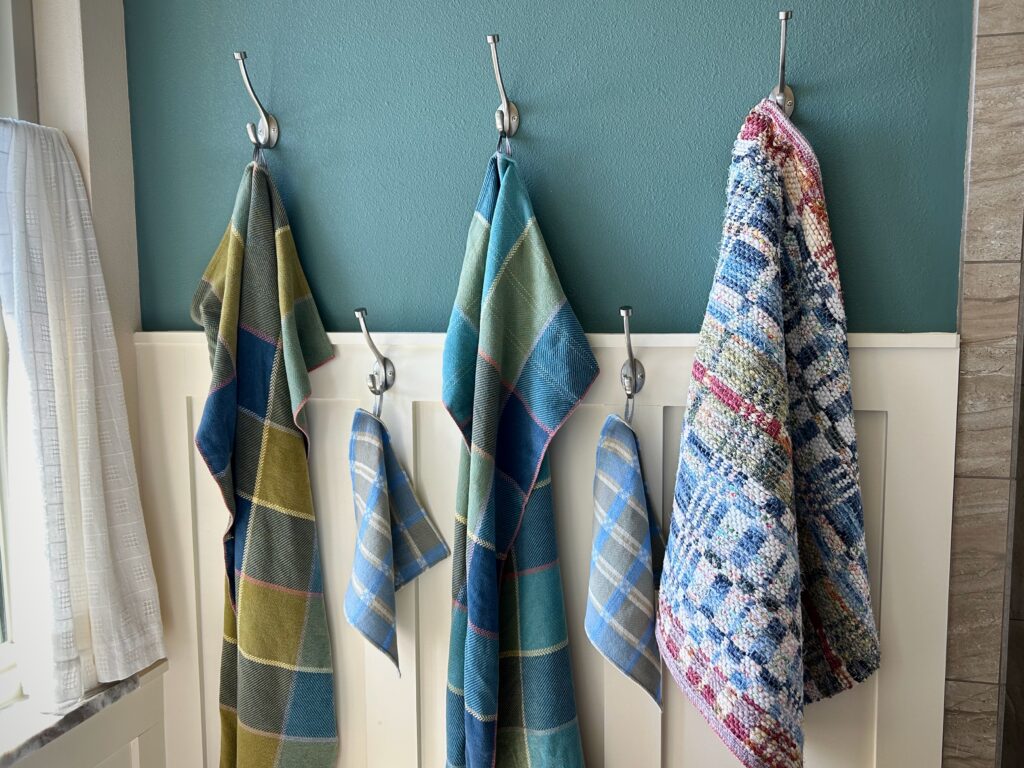
Happy Weaving!
Karen