Properly dressing the loom means no thread out of place, no crossed threads, no missed threads. Every linen end is threaded through a heddle on one of four shafts, following a draft for dice weave (pattern weft on a plain weave background). I insert each thread one by one in a specific order. My fingers are the only tools I use for this task, and I love touching and directing every single thread.
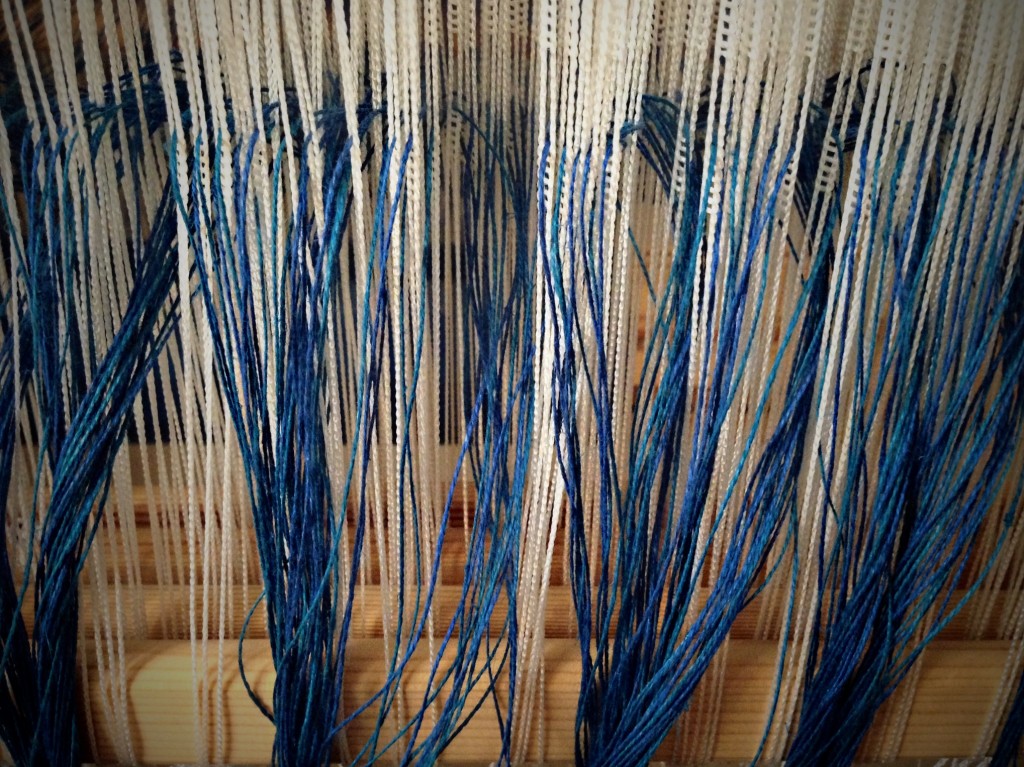
Someone great is looking after you. Our Father in heaven knows what is going on in your life, details and all. He knows the placement of every single thread in your personality. He knows the ins and outs of our needs, hurts, and desires. Father knows what we need before we ask. And yet, he invites us to ask. That’s a good invitation.
May you feel cared for.
Happy Threading,
Karen