How far will you travel? How will you know when you have arrived? Do you wish you could know when you are halfway there? Applied to weaving, I like to have the answers to these questions before I begin the “journey.” A pre-measured tape gives me consistency, especially important for multiple pieces in a set. The tape also acts as my “trip odometer.” I can see how far I’ve gone, and exactly how much is left to weave. It satisfies my insatiable need to know how close I am to the end. Are you like that, too?
How to Make and Use a Pre-Measured Tape
Supplies
- Roll of 3/4″ or wider twill tape (or any cloth tape or ribbon that does not stretch, and that pins easily)
- Tape measure with inches and/or centimeters
- Fine tip permanent marker
- Flat head pins
- Use the permanent marker to place markings on the twill tape, as measured with the tape measure. Mark the start line 1/2″ from the end of the twill tape, so that the tape can be pinned in front of the mark.
- After drawing a line for the starting point and ending point, draw a line at the midway point, labeled MID.
- Include dotted lines for hem measurements, if applicable. Write the hem measurement on the twill tape; i.,e., 3/4″ or 2 cm.
- Write the weaving length measurement on the twill tape. Include calculation for takeup, if desired; i.,e., 25″ + 3″.
- Write the project or item description on the twill tape, if desired, for ease of repeat use; i.e., handtowel.
- Add other lines or marks, as needed, for borders, placement of weft colors, or other design elements.
- 1/2″ after the final marking, cut pre-measured twill tape from the roll of tape.
With the warp under tension, pin the pre-measured twill tape near the right or left selvedge with two flat-head pins. Match the start line of the tape with the beginning of the weaving.
Before each advancement of the warp, move the pin closest to the breast beam to a point near the fell line. In this way, have the pins leapfrog each other, moving only one pin each time. Always keep the warp under tension when moving the pins.
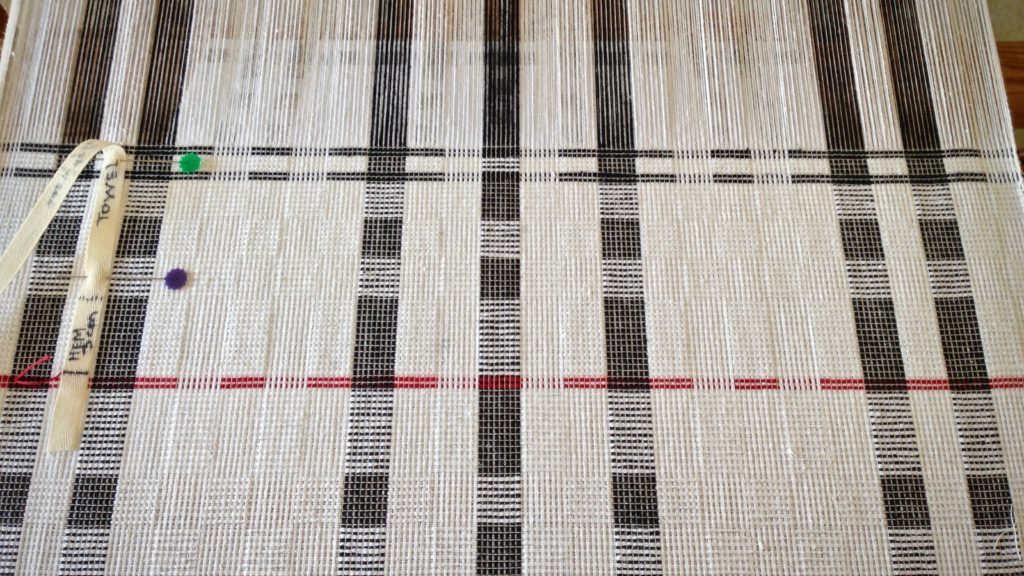
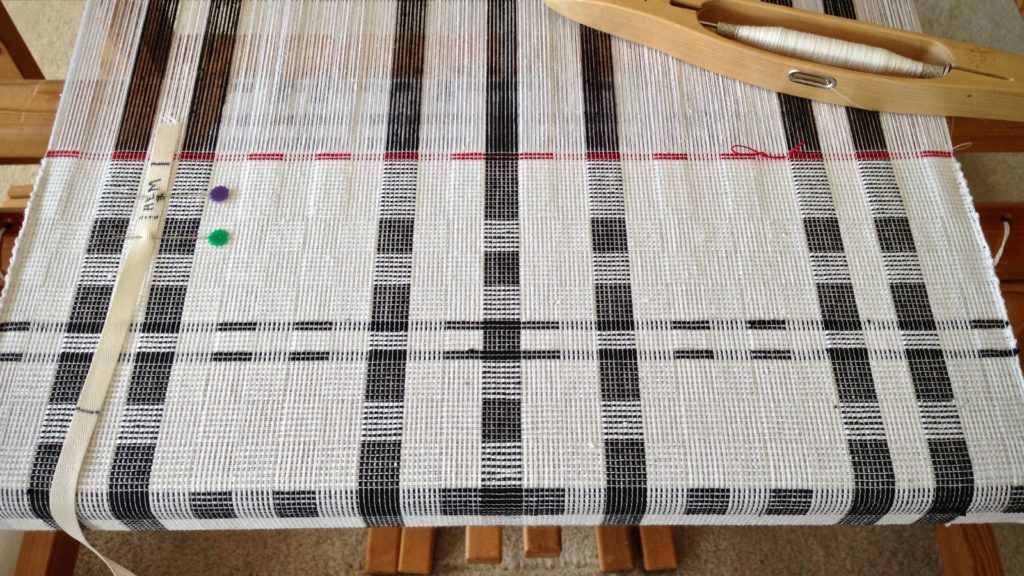
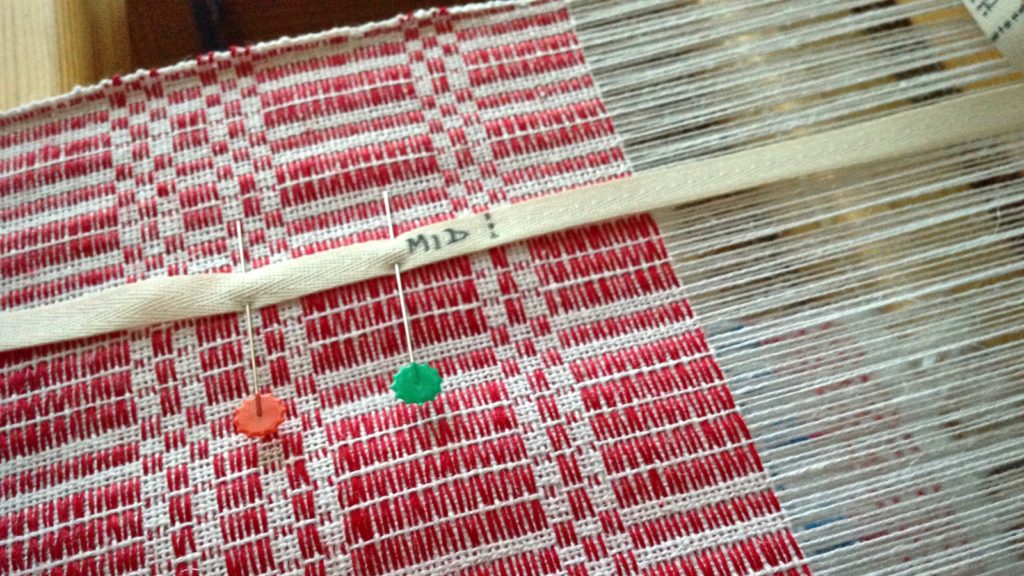
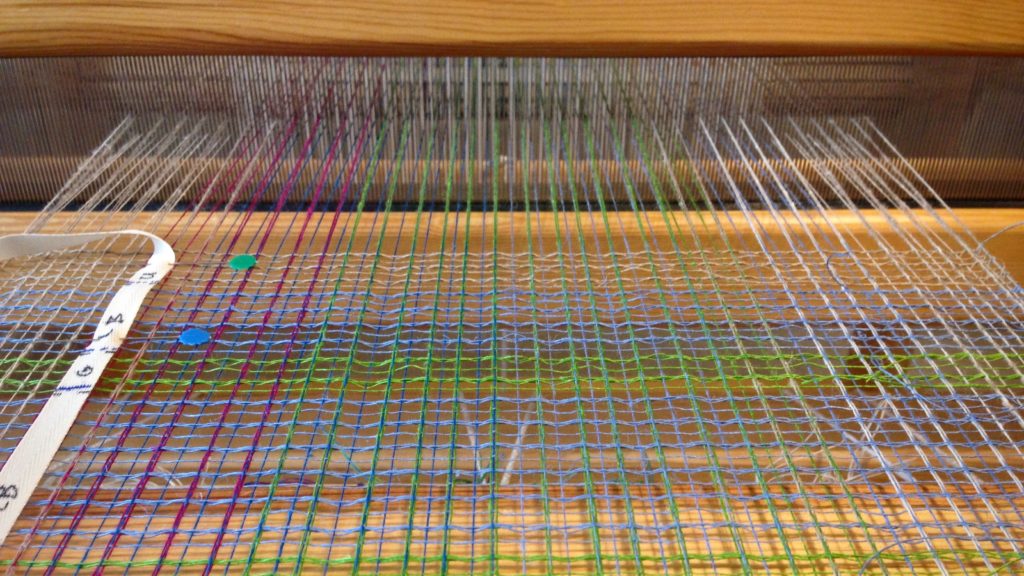
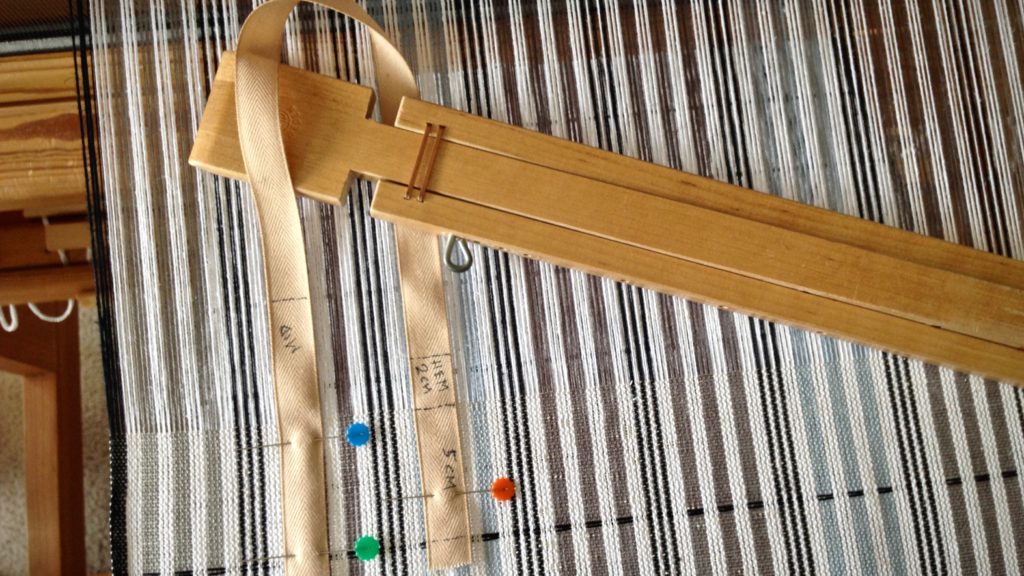
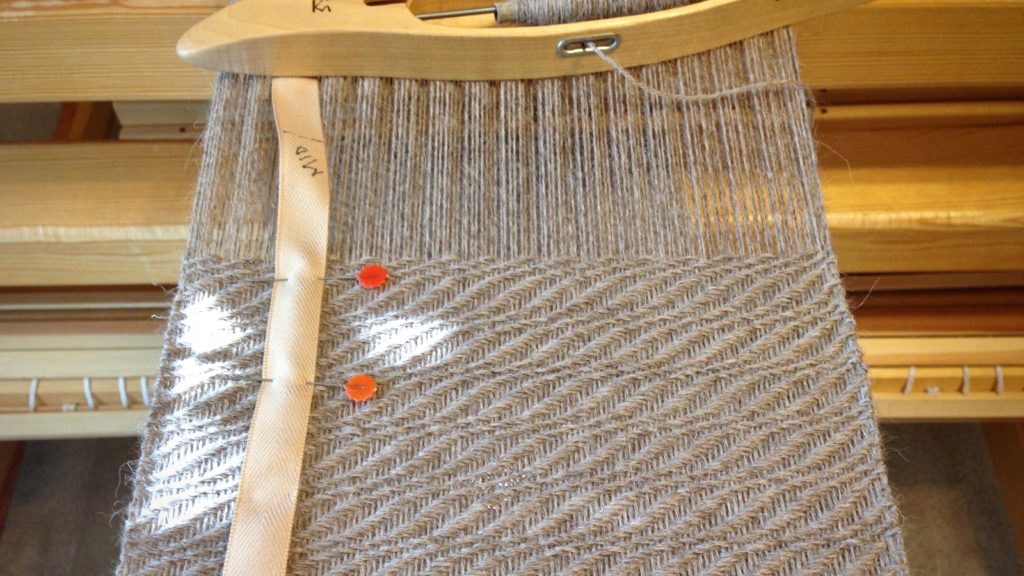
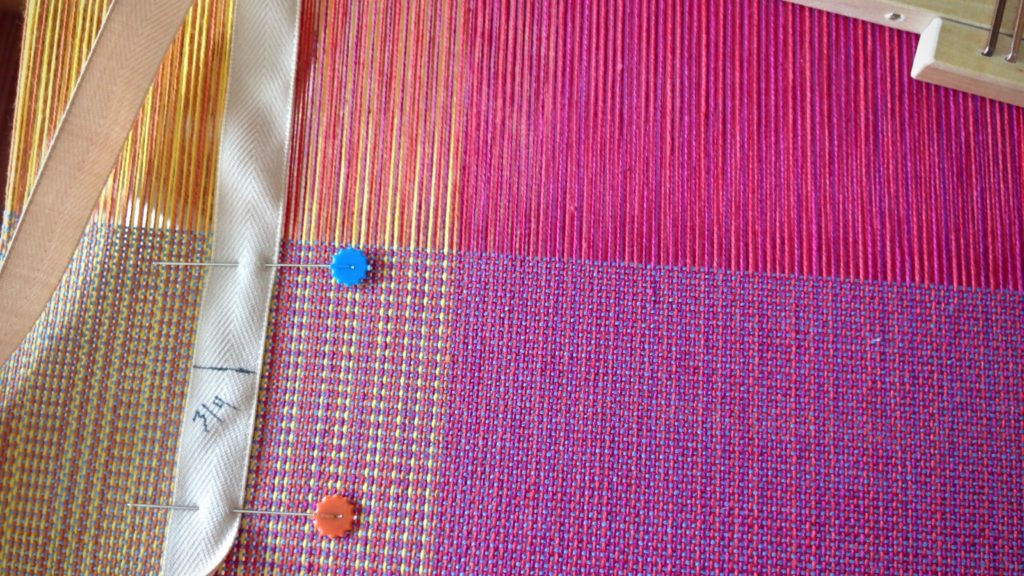
May you accurately measure your ways.
Truly yours,
Karen