I’ve been waiting for a bright sunshiny day to thoroughly examine this tightly-woven linen satin dräll fabric. Today is perfect. Fixing errors must be done before the fabric is washed, when the weave will become even tighter. I am looking for unwanted floats where the shuttle skipped threads, and for loops at the selvedges.
In my examination I did find an errant float and a few small selvedge loops. Let’s get started.
Tools:
- Blunt-tip needle. Sharp needle tip has been sanded to a rounded tip.
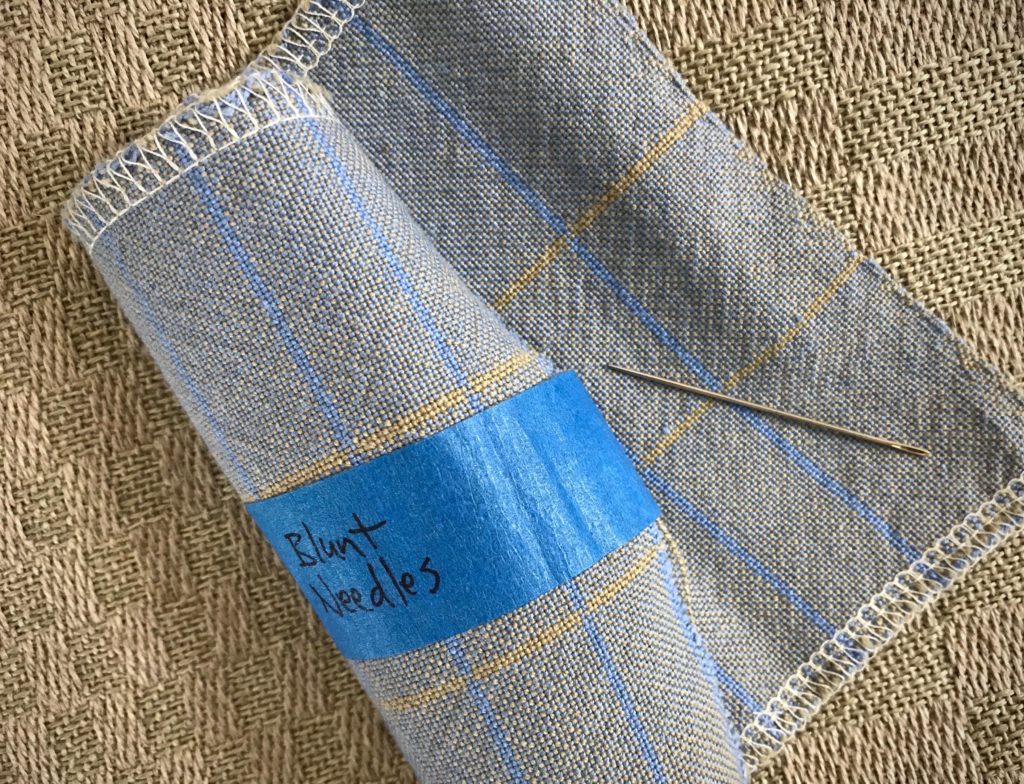
- Thread. Use the same weft or warp thread that is in the area needing repair.
- Good lighting. If the fabric has a complex structure, good lighting is essential.
- Magnification. I take a photo on my iPhone, and then zoom in to see the minute details.
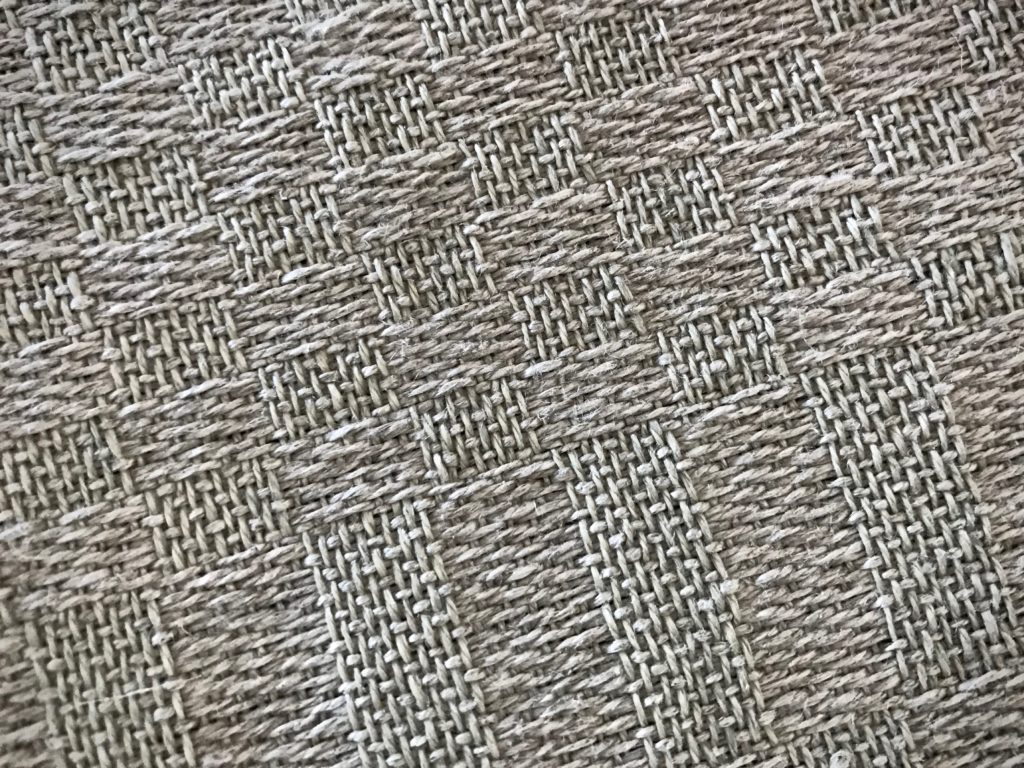
How to Mend Skipped Threads:
1 Locate the error. Here is a long weft float.
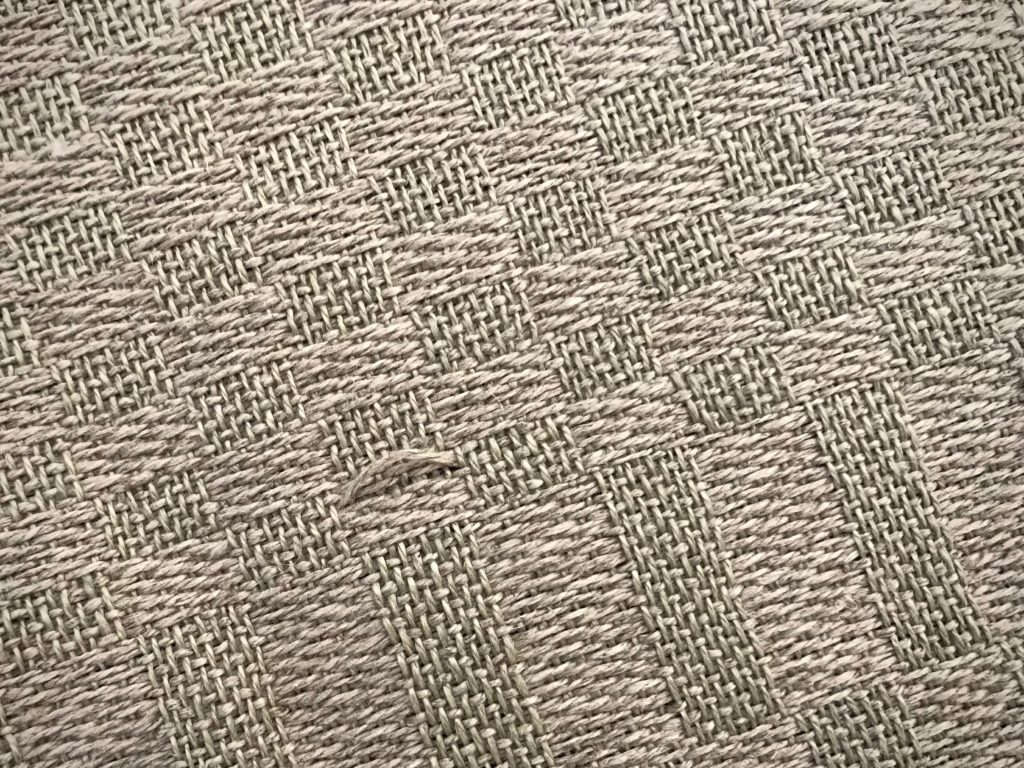
2 Thread the blunt-tip needle with a length of the same thread as the float.
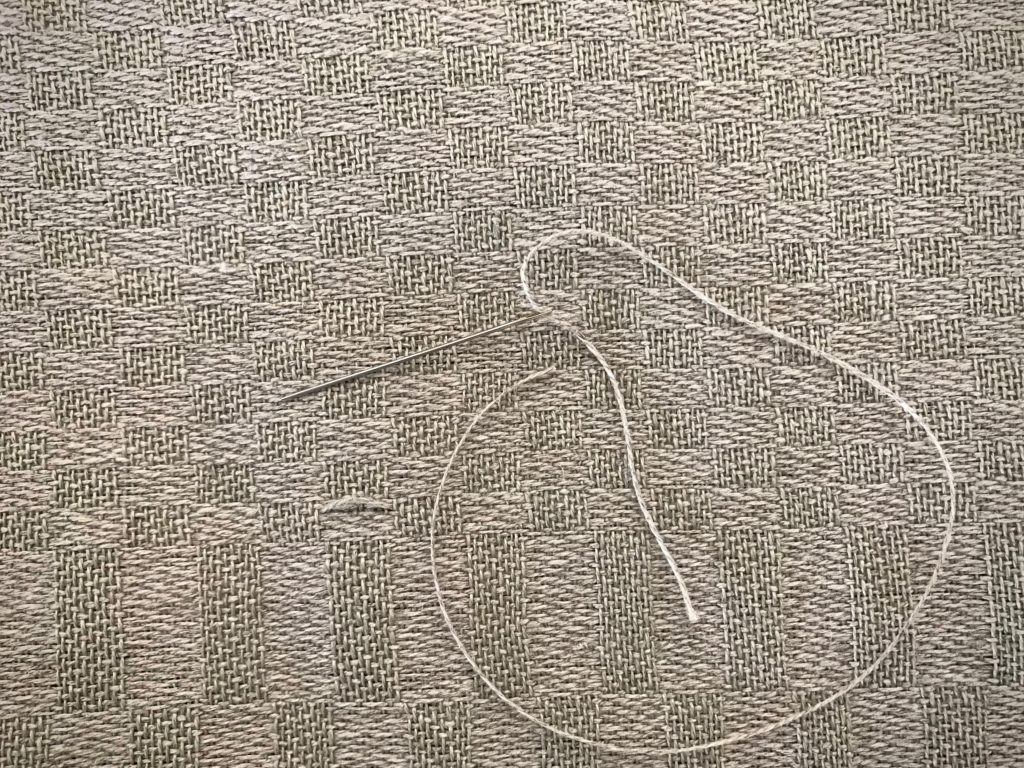
3 Following the exact under-over pattern of the weave, start one inch before the float and needle-weave toward the float. I lay my iPhone nearby, with the magnified iPhone photo clearly showing the weave pattern.

4 Needle-weave the correct path of the thread through the float area. Continue needle-weaving along the same thread pathway, going one inch beyond the float.
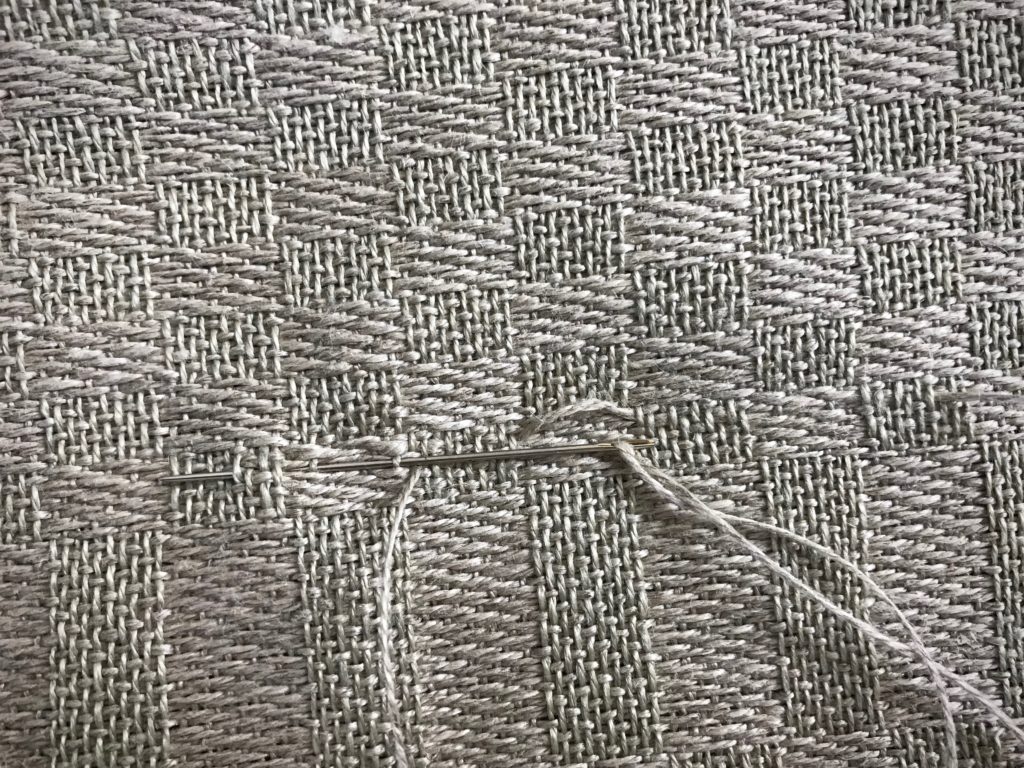
5 Check the front and back of the fabric to see if your stitches match the correct pattern of the weave.
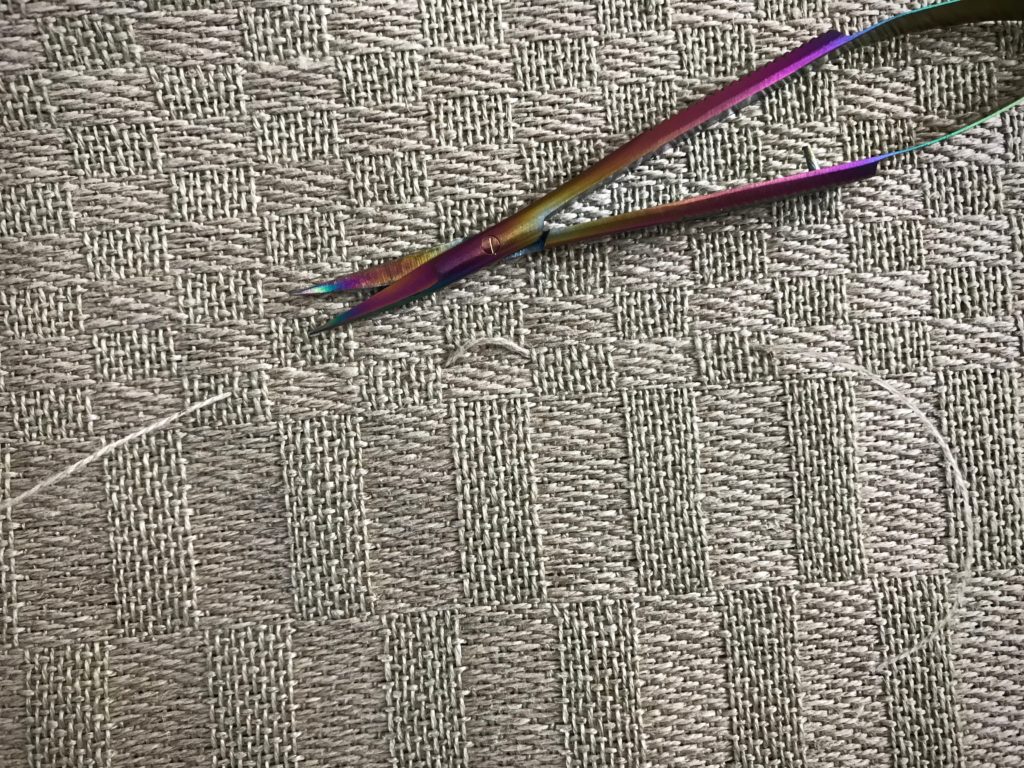
6 When you are certain that the float thread has been accurately replaced, clip the float and remove it (or, leave it and trim it after washing). Leave two-inch tails on the replacement thread, and trim after wet finishing. (I leave the replacement tails so I can find and check the repair after it is washed. This also allows for shrinkage before trimming.)
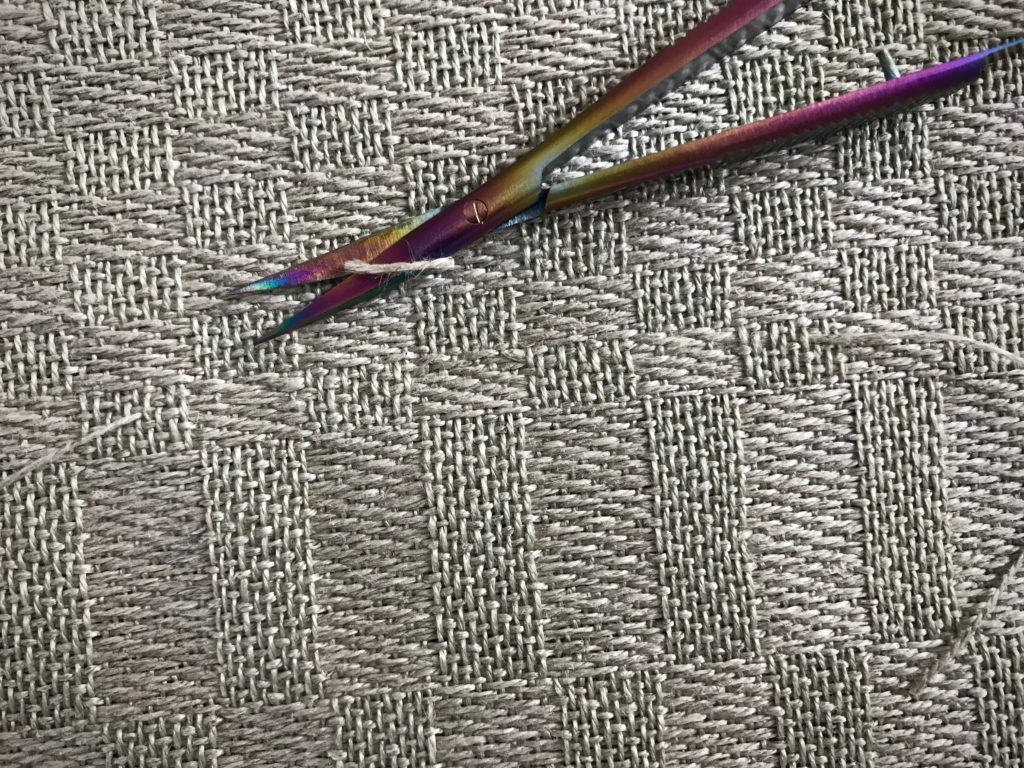
How to Fix a Small Selvedge Loop
1 Locate the loop.
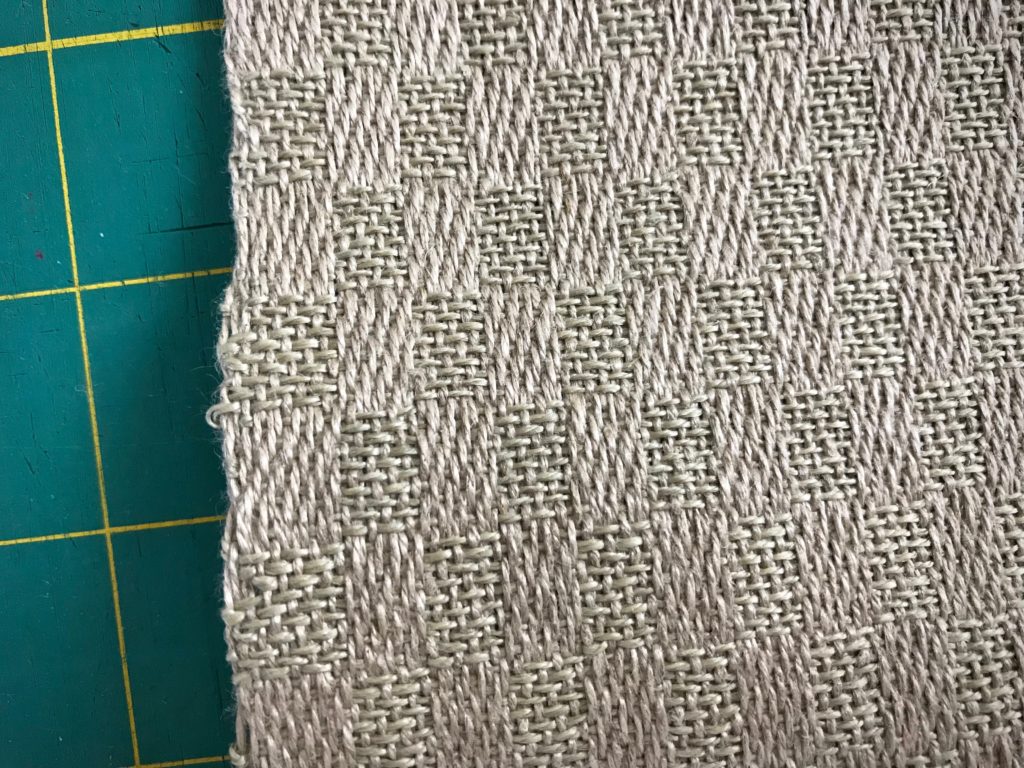
2 Using the blunt-tip needle, gently ease the excess thread to spread over four or five stitches inside the selvedge.
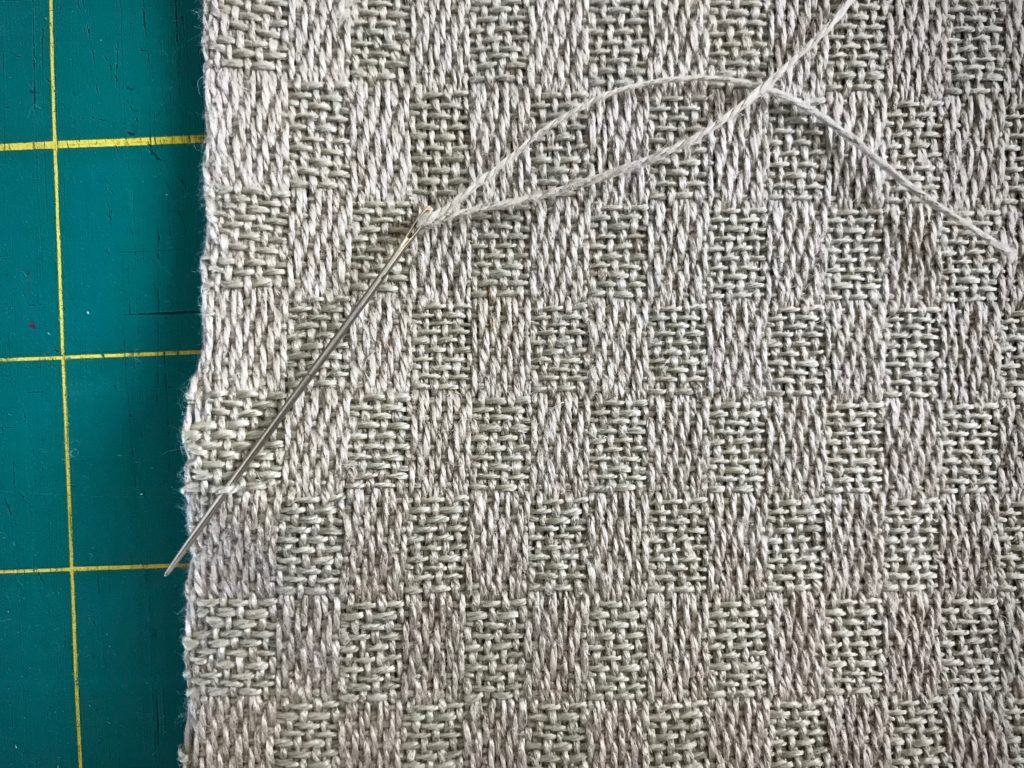
3 The thread that has been eased in (just above the needle) will completely smooth out in wet finishing.
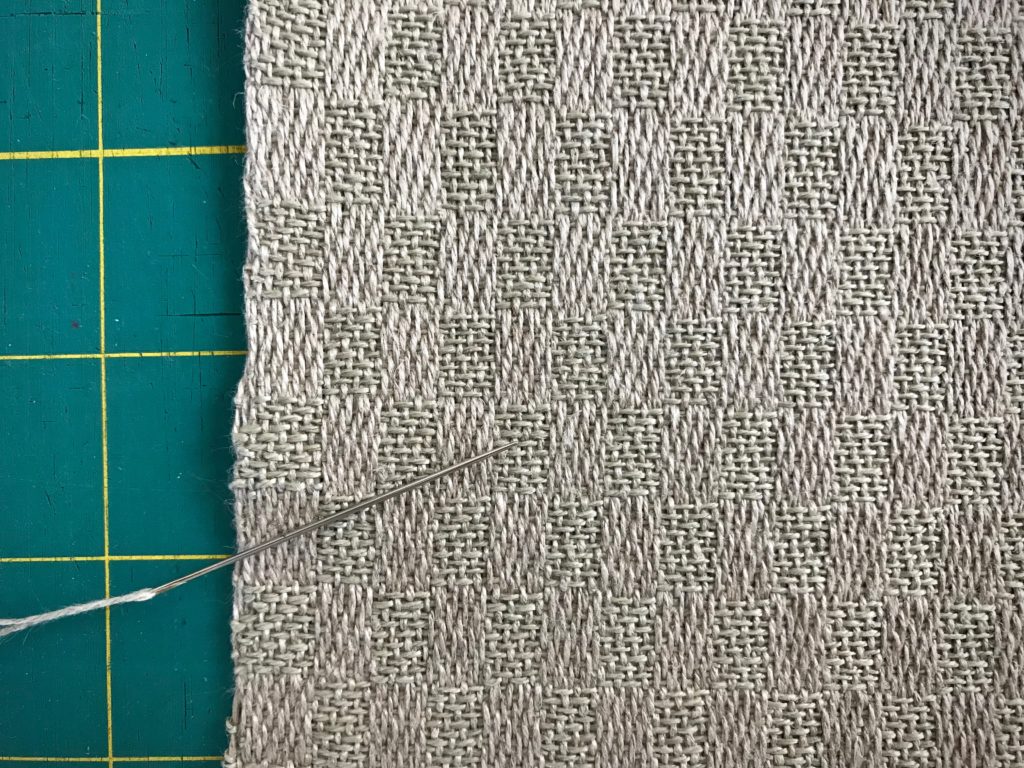
What skipped threads and loops would be found if I were examined this closely? Would I leave them and hope no one notices? Or, would I allow re-weaving and cutting away? A negative attitude is replaced with a thread of thankfulness. A loop of complaining is eased back in. The result is joy. A thankful heart knows joy. When the fabric is washed, the errant floats and loops are gone. What remains is the woven fabric with lustrous threads of joy.
May you have a bright sunshiny day.
With you,
Karen